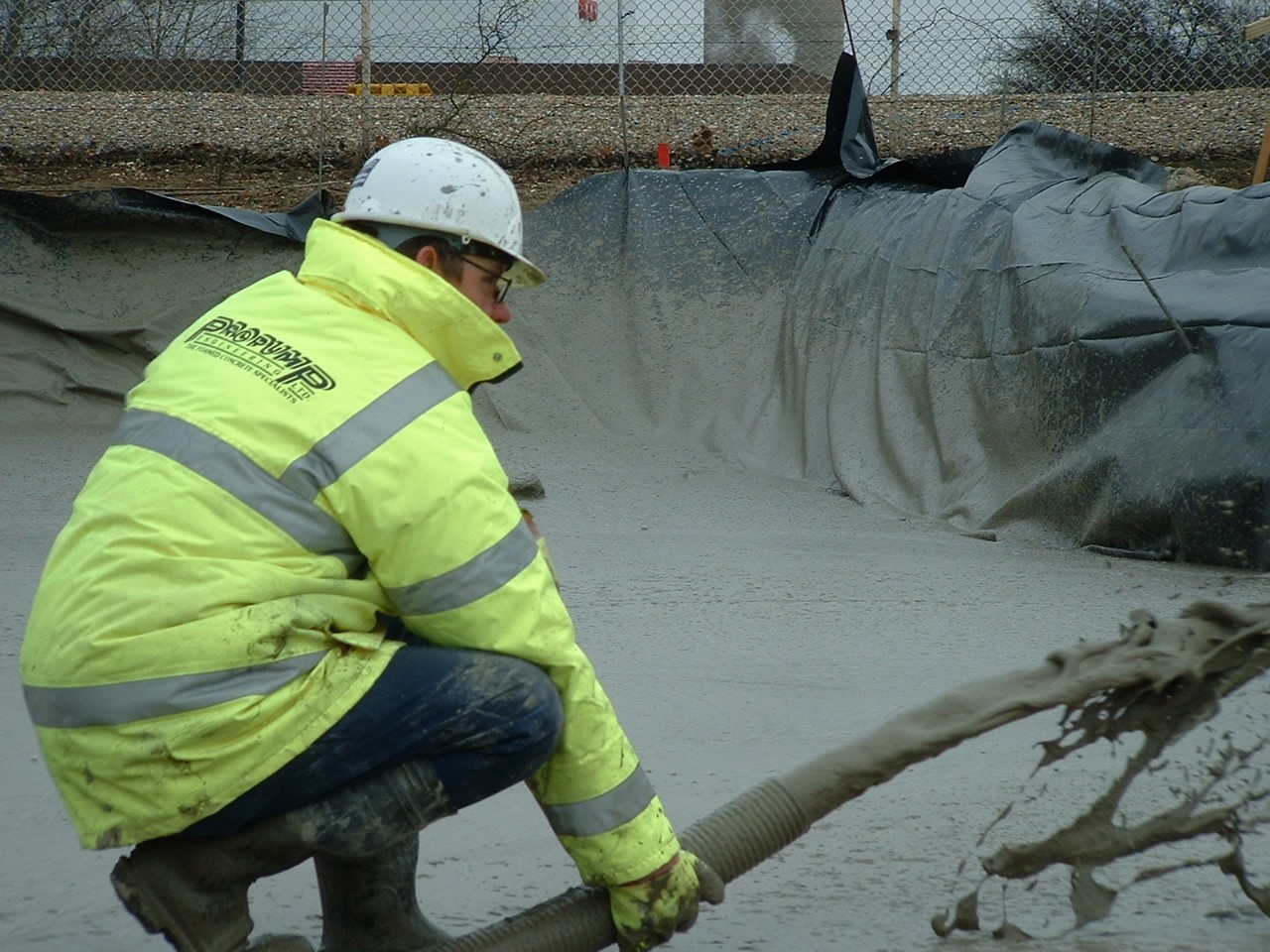
What is Foam Concrete?
What is foam concrete?
Foam concrete is an incredibly useful material used to produce large volumes of relatively low strength void filling material; it can easily be pumped long distances and will fill most cavities.
Foam concrete is very fluid and flowing, it will “search” without requiring levelling or compaction, Moreover, foam concretes will flow through trenches and encapsulate pipes, fittings and obstructions. Foam concretes are specified to reduce loadings, reduce site delivery numbers, and provide temporary, stable material for works as just a few examples.
Why is it called foam concrete?
A foam concrete is classified as a highly air entrained sand cement, or, cement only slurry with greater than 20% air by volume. “a cementitious material that consists of minimum 20 percent foam”. The mixes that Propump provide range from 20% – 85% by volume of foam. The majority of material provided by Propump has at least 50% foam by volume entrained.
Air is mechanically entrained using a pre-formed foam that is mixed with the cementitious base material to produce a lighter density, mixed material.
On site, foam concretes are typically produced with at least 50% by volume air entrainment, up to 85% depending on the mixes. Their densities range from 400kg/m3 to 1800kg/m3 with strengths ranging from 0.5n/mm2 to 12n/mm2
The name “foam concrete” can be a little misleading, a more apt description would be “foamed mortar” or “foamed Grout” other common names are “aerated lightweight concrete” and “cellular lightweight concrete” to name but a few.
What are the properties of foam concrete
Foam concrete is used primarily as a void filler, its high rate of expansion and fluid properties often make it a much more ecenomical filling material than stiff low cement concrete, or hardcore and loose materials that require compaction.
Pre-foam and Inline methods
PRE FOAM
This method of producing foam concrete can be completed on, or off site. Foam concrete is produced by part filling a standard ready mix concrete truck, the rest of the volume is then made up with foam, using the blades inside the “drum” to mix the material. Pumping would occur as a secondary operation.
ADVANTAGES
- Can be produced off site
- Requires only a basic foam generator
- Ideal for jobs requiring minimal foam
DISADVANTAGES
- Quality of mixing is subject to the quality of the mixing blades on the truck
- Volume will be lost during mixing and pumping so “over foaming” is required
- Densities recorded before pumping will be different to that delivered
- Difficult to change the foamed material mid load if there are any issues with density
- Inefficient method of transporting material to site. Will require many deliveries, at time only half full.
- Costly in the long run due to part load charges incurred by ready mix suppliers
INLINE METHOD
Inline foam concrete production can produce both light weight and heavier density foam concretes. Ready mix trucks carrying full payloads of material will be delivered to site. The inline foam generator and pumping system will pump the neat, base material, whilst injecting the foam, under pressure into the concrete lines, this material is then mixed through a series of in-line mixer plates.
ADVANTAGES
- Only full mixer deliveries minimising total number of deliveries
- No part load charges for un-carried materials
- Complete foam production and pumping solution
- Continually adjustable density (throughout one load if required)
- Possible to produce materials from constituent parts (on site silo batching)
- Overall quicker production and delivery rate of finished products
- Able to provide a separate pre-foam solution if required
DISADVANTAGES
- Complex, bespoke machinery required
- Equipment can be expensive to operate and maintain
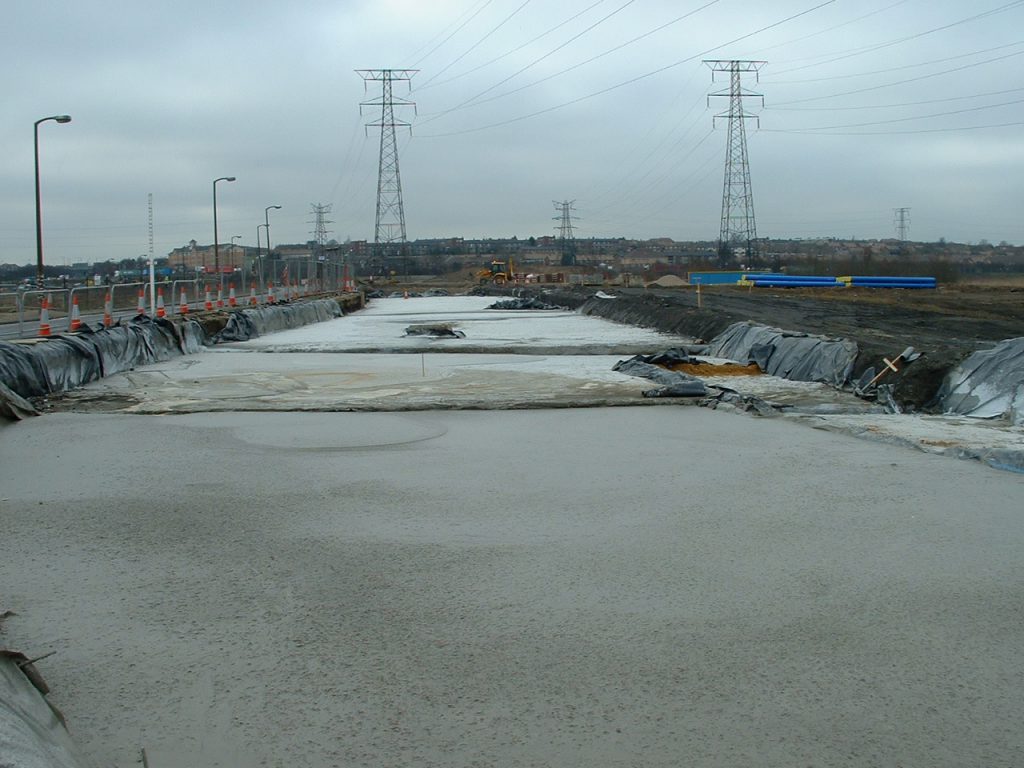
Foam concrete base mixes
Base mixes for foam concretes differ to a typical “concrete” a foam concrete will use sand, cement, and water.
The cementitious content, either classed as CEM1 or Ordinary Portland cement is used, however cementitious materials such as Pulverised Fuel Ash and Ground Granulated Blast-furnace Slag can be used in various quantities, their use depends on local availability as well as the reaction level to the various foaming agents used.
Why do foam concretes have so much cement?
A foam concrete base mix will have a much higher cement content (minimum 350kg/m3 – 1200kg/m3) compared to a standard “concrete” mix for slabs or even structural concrete. The reason for this is at least two fold.
- Air reduces the strength of concrete exponentially
- Water reduces the strength of concrete, linearly
A foam concrete mix will typically have a higher water content than a traditional concrete, in order for it to be pump-able and mix with foam. Not only this but historically Water reducing agents or plasticisers do not mix well with foaming agents.
The production of foam requires a surfactant or foaming agent to be diluted into water before being foamed, typical expansion for a protein based “dry” foam is 20 x. foaming agent is diluted at 3% – 5% with water before being agitated through a “cigar” to produce a stable foam matrix.
Why do foam concretes have no aggregate or stone?
In order to produce a uniform, homogenous, the material needs to be thoroughly mixed there needs to be minimum “drop out” or segregation of aggregates. With the addition of high volumes of air and water, stones and other large aggregate would simply fall to the bottom of the mix, creating a large deviation of mix constituents and thus an inferior finished product. Having a maximum of 5mm sand means that all the binder and filler is kept in suspension around the foam as the cement hydrates and cures.
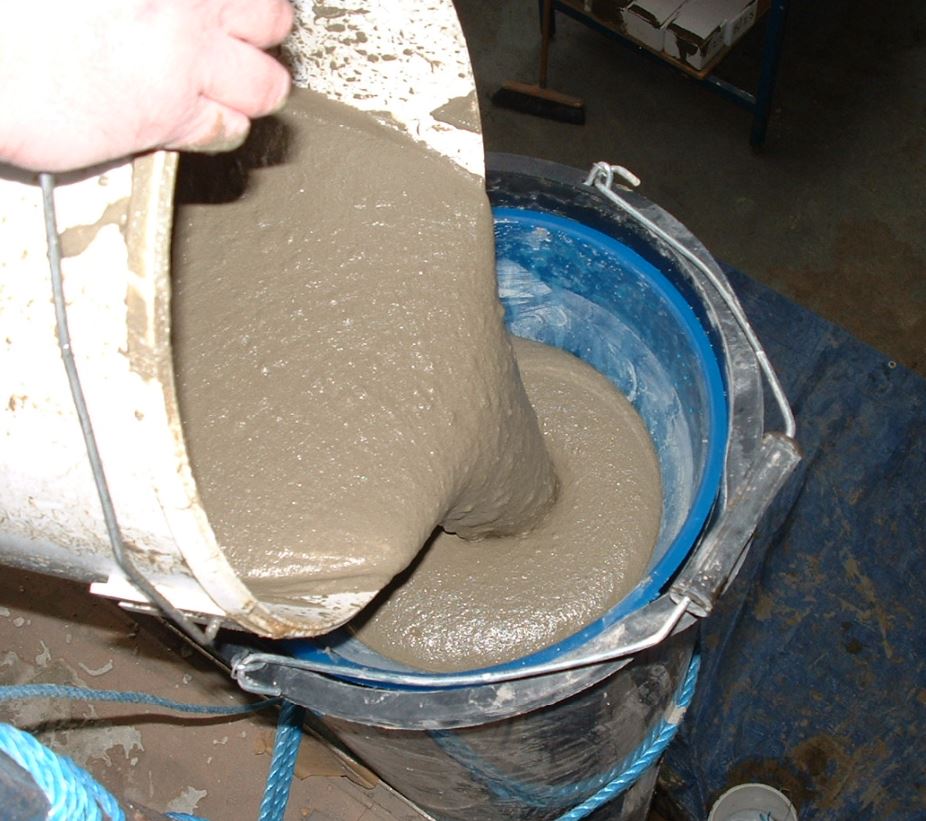
More information
Propump Consultancy Services
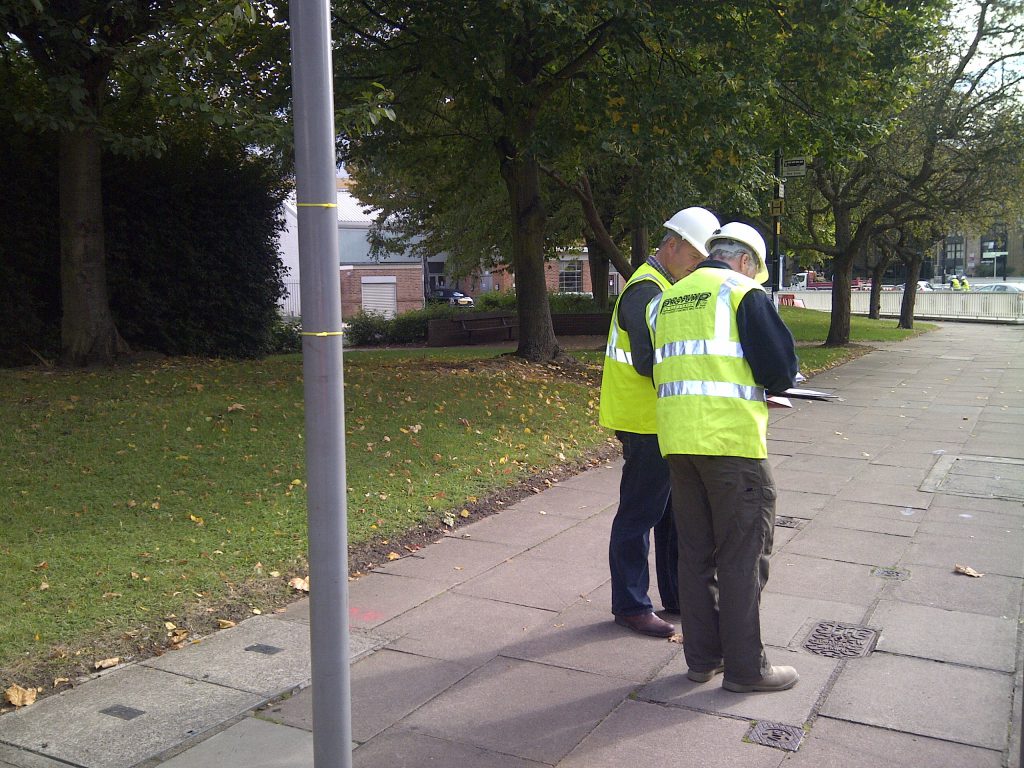
Propump news & articles
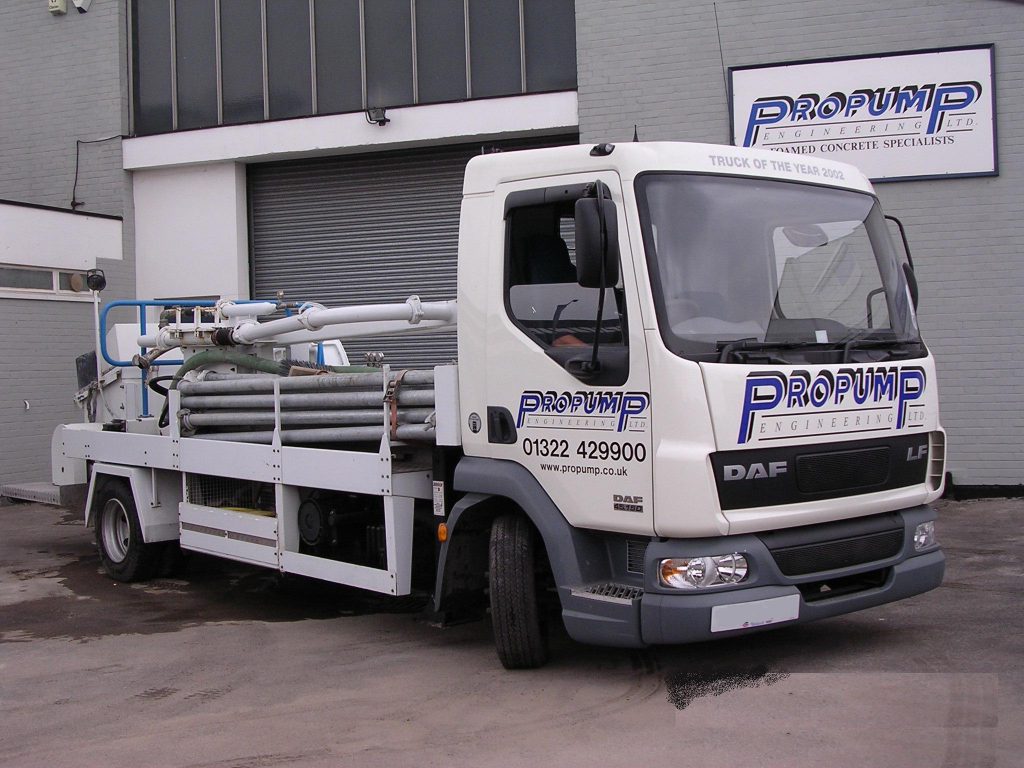
Why choose foamed concrete?
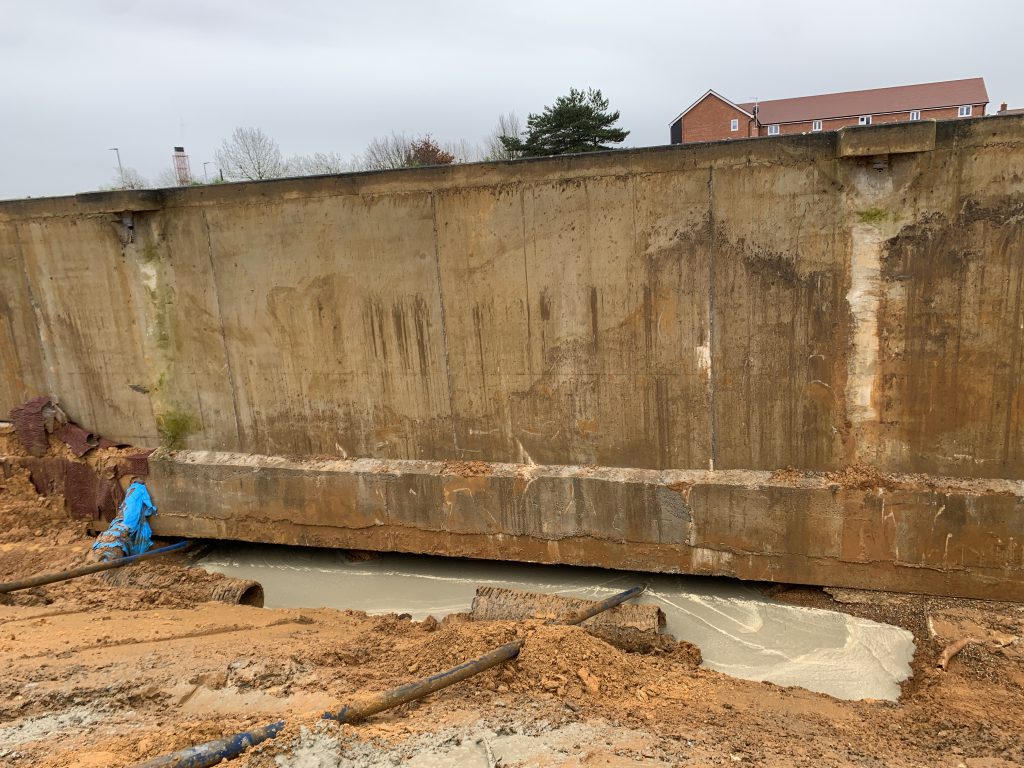
Projects by Propump
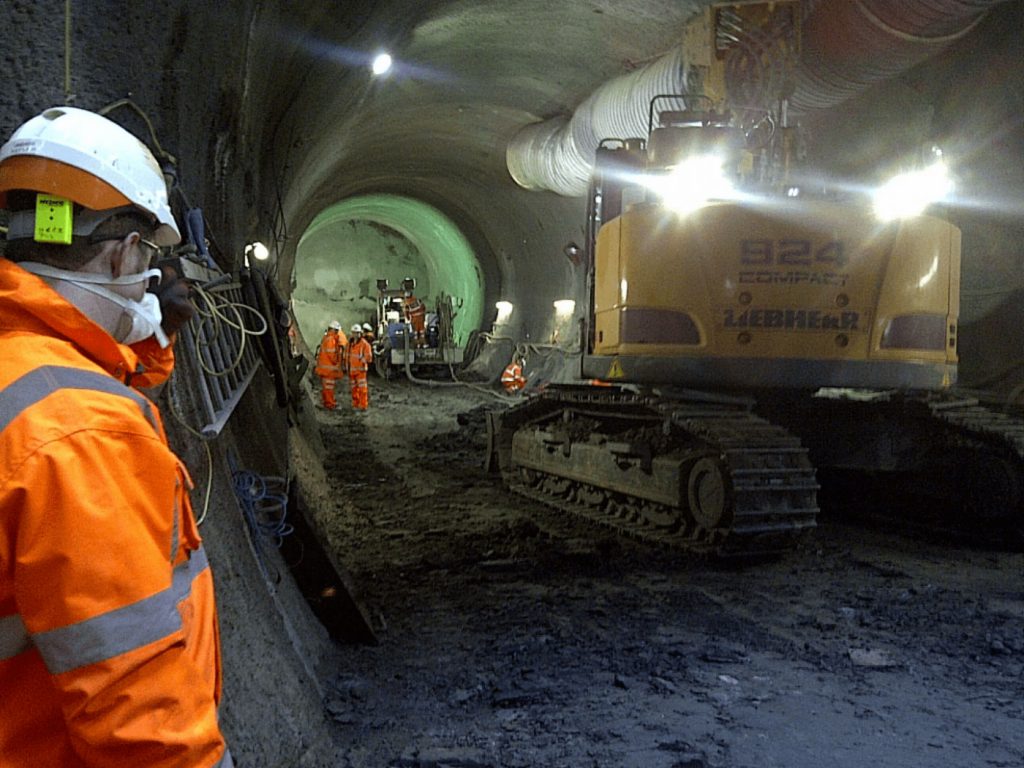
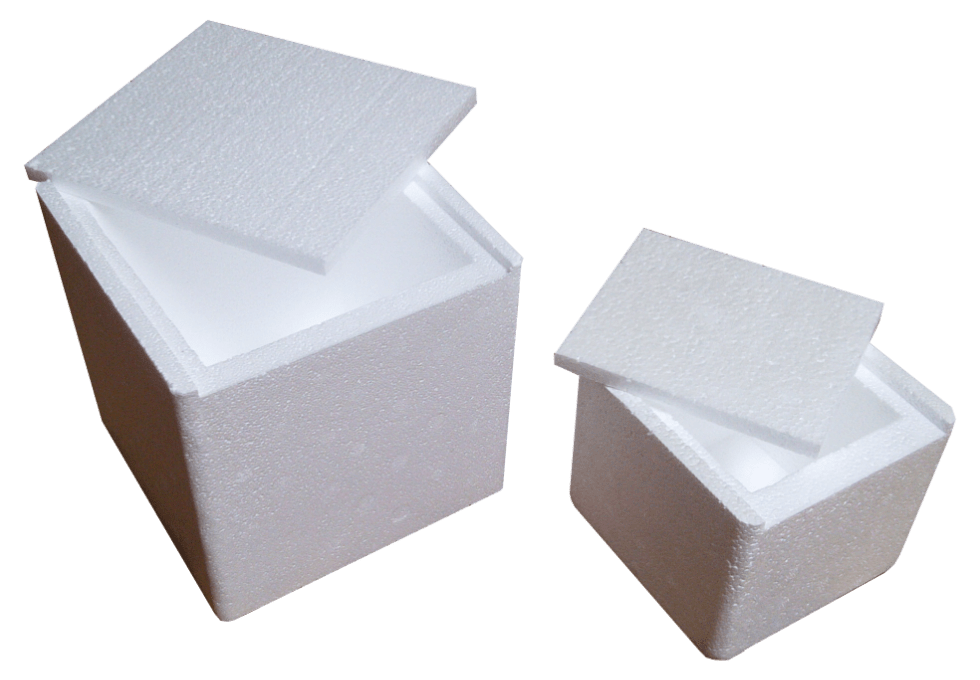
Foamed concrete cube moulds
Large quantities of both 100mm and 150mm foamed concrete cube moulds are kept in stock, available to purchase on a next day delivery.
Please call the office for up to date prices on 01322 429 900 alternatively email info@propump.co.uk